Achieving Success with Offsite Construction
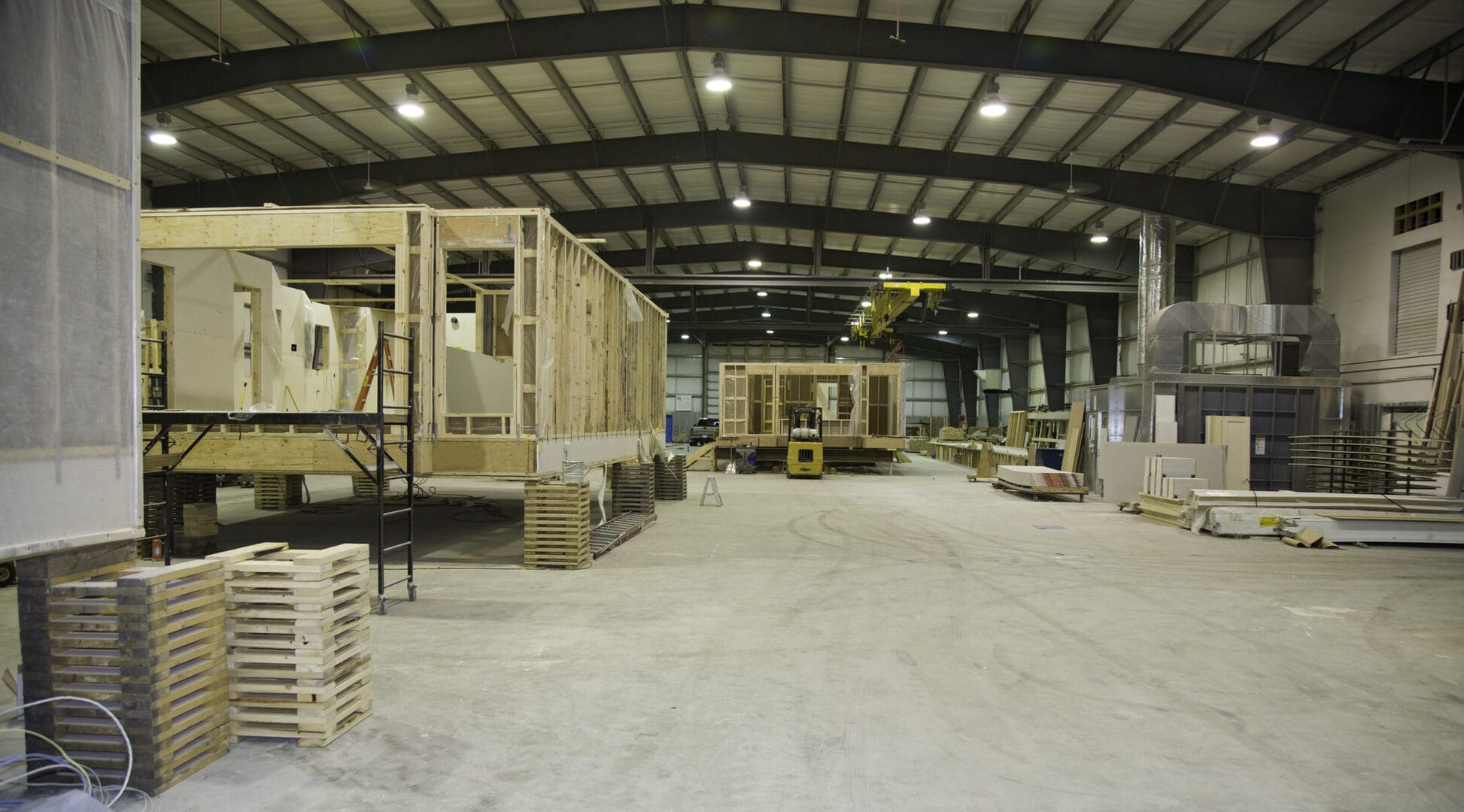
- A keynote presentation directed to construction owners that will be focused on the benefits of truck shippable module solutions.
- Identifying, planning and managing critical milestones on an offsite / modular project. This presentation will dive into what an owner should look out for as a project progresses, and how milestones are managed on different-sized projects. It will be given by Bill Lewis, SABIC, and Paul Hochi, Worley.
- Pre-stressed/pre-cast concrete uses, and its advantages. This session, led by Bob Pool, Alfred Miller Contracting, will include success stories.
- A presentation on a design assist approach to a truckable modularized utility systems will be given by Brad Hughes, Epsilon Industries Inc.
- A roundtable discussion on cost certainty and budgeting (in a Q/A format) will be led by Teresa Magnus, Magnus & Co., Inc., and Kevin Shipp, McAbee Construction.
- Steve Lehew, Chemours, will share how modular construction provides opportunity for “concurrent” offsite and onsite work activities, which results in significant reduction in the overall project schedule.
- Finally, FMI will present insight from their megatrends research and a high-level FMI/CURT/CII offsite construction study called New Day, New Mindset: Rethinking Offsite Construction.
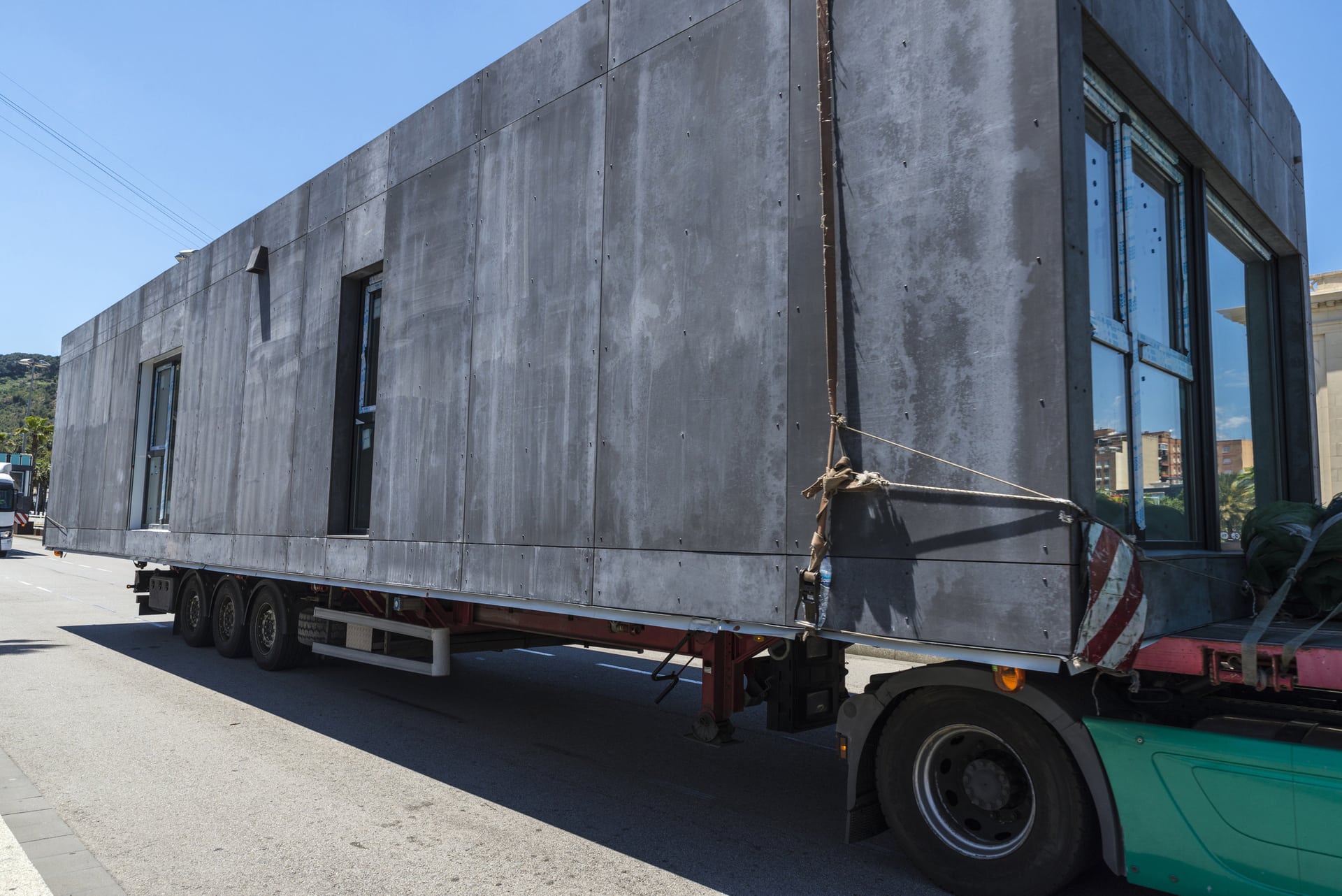
November workshop on offsite construction will focus on truck shippable modules, and how owners can use offsite construction to complete projects on time and on budget.
Using offsite construction contractors can build anything from individual components to an entire building in a different location than the final site. Controlled environments impact everything from scheduling, to efficiency, to safety, to budgeting.
According to the Modular Building Institute, modular construction goes hand in hand with offsite construction – components of the building are constructed offsite, in controlled plant conditions, using the same materials and designed to the same codes – but in half the amount of time. Check out this video of a fast-track schedule hospital that was built in New York City with over 59 modules:
Globally, prefabrication and off-site construction have provided many productivity benefits, including combatting labor shortages and scheduling issues, reducing costs, and increasing quality and safety. According to a recent report, the global modular construction market was valued at approximately USD$111 billion in 2018, and it’s expected to generate around USD$175 billion by 2025.
While popular overseas, prefab and offsite are only now emerging as a trend in the United States; albeit, one to take seriously. As the construction workforce ages and competition for skilled workers increases, companies will need to think outside the box to get projects done – or risk becoming obsolete. “Our industry has a lot of work coming and not a lot of workers, so we have to come up with alternatives of how to address that,” says Mike Brewer, Global Capital Materials Management at Freeport-McMoRan, Inc. “The modular yard seems to be among the best solutions you can look at.”
Mike is Co-Chair of CURT’s Offsite Construction Committee, alongside Bill Lewis, Senior Manager, Projects Construction, Global E&PM, for SABIC. The Committee is in the process of planning its annual Offsite Construction & Modularization Summit, which will be held in Clearwater Beach, Florida on Tuesday, November 6, 2019. This is the third summit CURT will host on this topic, with this year’s theme – Truck Shippable Modules – geared towards overcoming challenges and sharing best practices related to planning, budgeting and executing projects. A secondary theme will look at Complex Process Modules.
Building from these themes, focus will be on all sizes of “truck shippable modules,” and what those working in various industries, including oil and gas, mining, chemical, automotive, pharmaceutical, alternative energy, and food and beverage, need to know about shipping modules to their construction sites.
Topics discussed will include:
- A keynote presentation directed to construction owners that will be focused on the benefits of truck shippable module solutions.
- Identifying, planning and managing critical milestones on an offsite / modular project. This presentation will dive into what an owner should look out for as a project progresses, and how milestones are managed on different-sized projects. It will be given by Bill Lewis, SABIC, and Paul Hochi, Worley.
- Pre-stressed/pre-cast concrete uses, and its advantages. This session, led by Bob Pool, Alfred Miller Contracting, will include success stories.
- A presentation on a design assist approach to a truckable modularized utility systems will be given by Brad Hughes, Epsilon Industries Inc.
- A roundtable discussion on cost certainty and budgeting (in a Q/A format) will be led by Teresa Magnus, Magnus & Co., Inc., and Kevin Shipp, McAbee Construction.
- Steve Lehew, Chemours, will share how modular construction provides opportunity for “concurrent” offsite and onsite work activities, which results in significant reduction in the overall project schedule.
- Finally, FMI will present insight from their megatrends research and a high-level FMI/CURT/CII offsite construction study called New Day, New Mindset: Rethinking Offsite Construction.
The Winter 2019 issue of CURT’s magazine The VOICE featured offsite/modularization as its cover story. In that article, Jim Peckham, a retired construction manager, noted that moving work offsite will help companies stay competitive, on schedule and on budget. He says, “The move to modularization, wherever it makes sense to do so, is something that needs to be considered in order to remain competitive in completing projects on schedule and within budget. It is quickly becoming clear that shifting the work offsite is – in many cases –the ideal solution that’s needed to accomplish this.” You can read the full issue here.
There are many benefits to offsite construction, including more projects that are completed on time and on budget with excellent safety records. If your company is interested in learning more about the benefits, you can register for the Offsite Construction & Modularization Summit here. Upon completion of the Workshop day, attendees are eligible for 6 CEU hours.
If you need help registering, or for sponsorship opportunities, contact Ronna DuBro at 513-981-2773, or by email at rdubro@curt.org.
CURT’S MISSION IS TO CREATE A COMPETITIVE ADVANTAGE FOR CONSTRUCTION USERS. CURT ACCOMPLISHES THIS MULTIFACETED OBJECTIVE BY PROVIDING AGGRESSIVE LEADERSHIP ON THOSE BUSINESS ISSUES THAT PROMOTE EXCELLENCE IN THE CREATION OF CAPITAL ASSETS.