New Study: Top 5 Factors Impacting Construction Project Schedules
By Tim Negris, CMO, and Jason Lyon, Vice President of Customer Success, MOCA Systems, Inc.
MOCA Systems, Inc. recently used data from the Touchplan® production planning platform to analyze over 321,042 committed activities over the last 12 months to identify what issues are having the biggest impact on construction project schedules.
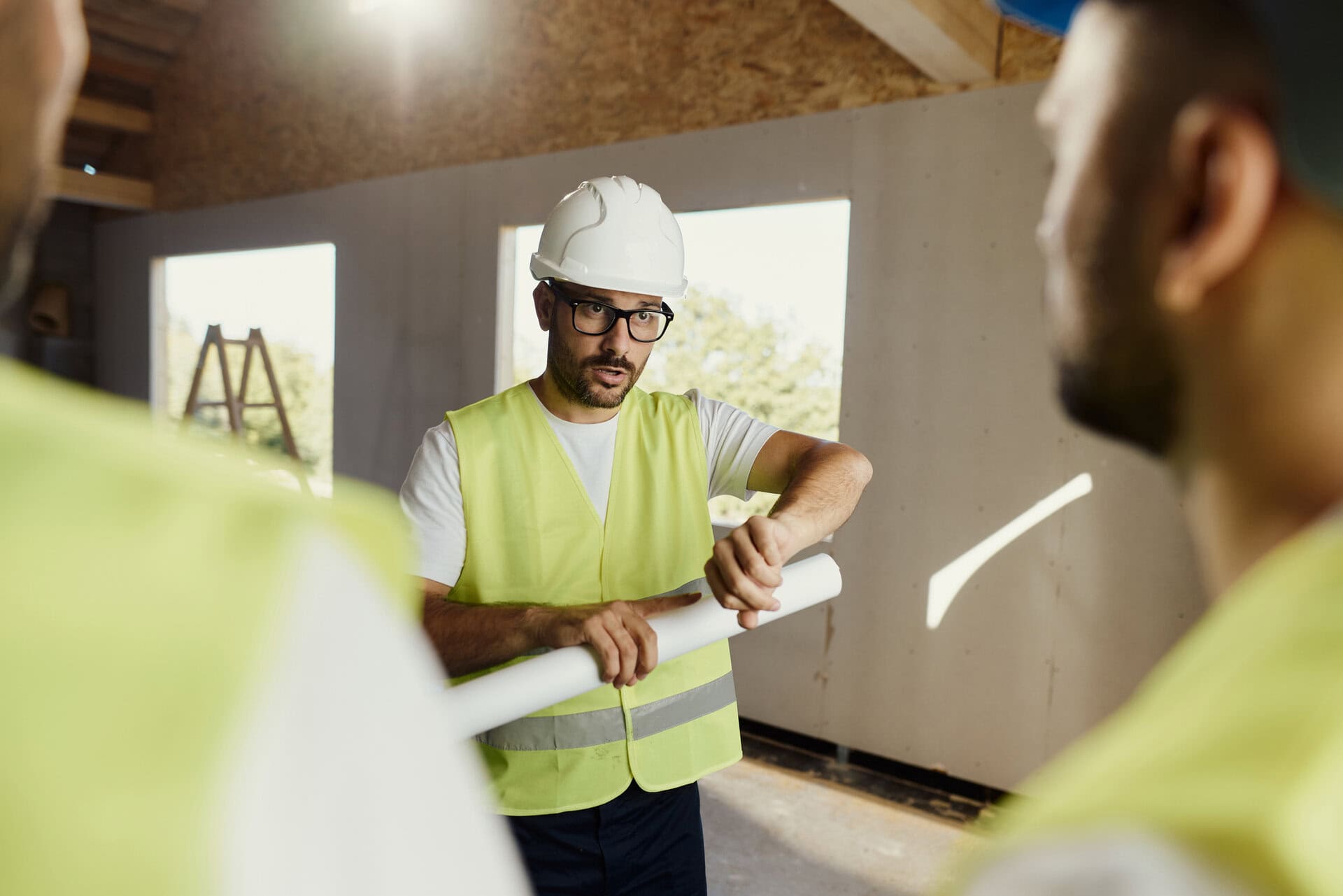
Key insights – Top schedule variance reasons
- Schedule variances related to handoffs are the number one reason for delayed activities, with over 168,000 reported issues.
- Variances related to staffing/crew/manpower are the second highest reported variance reason, indicating the impact of the skilled labor shortage on project schedules.
- Material/equipment-related issues are the third most cited reasons for activity delays.
- Design issues/changes cause variances in the schedule and have the fourth number of reported issues.
- Weather follows closely behind design issues/changes as the fifth largest variance reason reported.
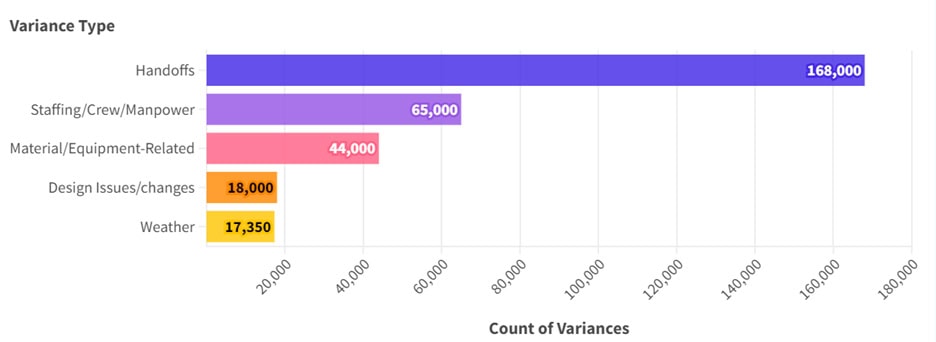
What are variance reasons?
Variance reasons are explanations for why a planned activity that was committed to finish on a certain date was not completed as planned. Originating from the Last Planner System®, the practice of tracking variance reasons stems from the fundamental Lean principle of using data to continuously learn, improve planning, and ultimately deliver projects on time and under budget.
For example, “predecessor not ready” is a common variance reason indicating that the preceding work was not finished in time for the next activity to start. This leads to delays and requires replanning to get back on track.
The following is an analysis of the top reported variance reason types: handoffs between disciplines, staffing/crew/manpower, material/equipment-related, and design issues/changes.
Jason Lyon, Vice President of Touchplan Customer Success, provides details about each of the top categories.
Handoffs between disciplines
Handoffs between disciplines are the number one reason for delayed activities, accounting for over 168,000 reported issues.
Poorly executed handoffs between disciplines are the leading cause of delays, severely impacting the master schedule in commercial construction projects.
For general contractors (GCs), this means extended deadlines, increased costs, and disrupted project timelines. Improving handoff processes is crucial to maintaining the master schedule, ensuring timely project completion, and enhancing overall efficiency and profitability.
“One of the cited variances that went into handoff variances was ‘predecessor not ready,’ which is a good example of waiting on the trade ahead to finish their work. This screams handoff. It’s the transition point where one trade partner completes their work, and another begins. When these transitions aren’t managed well, it leads to delays,” says Lyon.
Along with delays, when handoffs are not planned or executed properly, they lead to worker congestion and rework, which hampers overall productivity. As Lyon noted, “Missed handoffs equal replanning, and replanning creates more time spent in planning meetings. You have to work through the challenges that are created as a result of missed handoffs.”
Staffing/Crew/Manpower
Staffing/crew/manpower issues resulted in 65,000 variances.
“The construction industry is grappling with a persistent shortage of skilled labor that is driving up costs and delaying projects,” says Lyon. “With rising labor demands and no immediate workforce solutions, contractors must proactively ensure tasks are performed efficiently and disruptions are minimized through proactive, collaborative planning practices.”
Insufficient staffing and improperly planning manpower leads to missed deadlines that can severely impact project progress. Addressing staffing variances requires ensuring that teams are optimizing the flow of labor by sequencing activities in the most efficient order possible and collaboratively planning crews with those who will be completing the work.
Material/Equipment
Material/equipment-related issues caused 44,000 variances.
“Material and equipment-related issues often stem from delays in the delivery of supplies or machinery,” says Lyon. “When materials or equipment aren’t available as planned, it causes significant disruptions and delays in the project schedule.”
With critical materials like switchgear taking a year or more to arrive on site, teams need to address long lead items in their schedules as early as possible to minimize potential delays. Proper management of materials and equipment, and the ability to sequence work around their delivery, are essential for preventing these variances and keeping the project on track.
Design Issues/Changes
Design issues/changes led to 18,000 variances.
“Design issues or changes often result in rework and delays. When there are discrepancies or modifications in the design, it leads to confusion and requires additional time to address these changes, impacting overall productivity,” says Lyon.
Addressing design issues promptly and ensuring clear communication about any changes can minimize the impact on the project timeline.
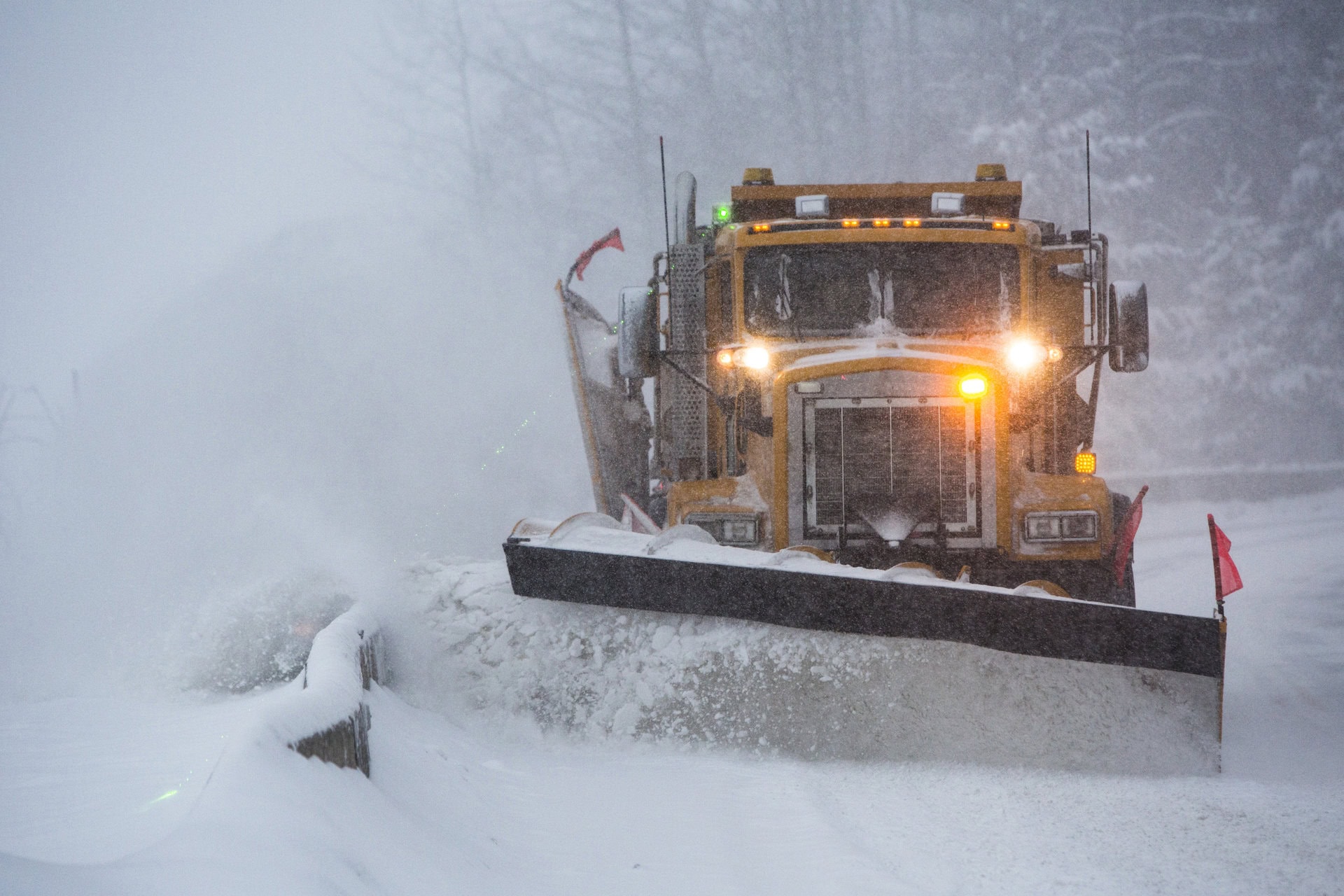
Weather
Weather-related events caused 17,350 variances.
Weather variances in construction refer to delays or disruptions in the construction schedule caused by adverse weather conditions. These variances can impact labor productivity, material delivery, and overall project timelines.
“The construction industry is extremely vulnerable to delays due to weather events,” says Lyon. “Heavy rain, high winds, and extremely high or low temperatures can put work on hold.”
Although no team can control the weather, proper planning for upcoming weather issues can mitigate impacts on the schedule. This means teams need a real-time, digital platform to re-sequence activities when weather impedes work. This proactive approach ensures that teams do not need to scramble on the day of an event to adjust activities, thereby maintaining project momentum and reducing potential delays.
Methodology
Over the past 12 months, 321,042 total committed activities have been captured in Touchplan. To track the status of these, users regularly update the completion dates of their activities. If a task is completed early or late, users must provide a variance reason. These variance reasons allow teams to explain why the work was not completed on time, and give context to any delays or early completions.
The data in this report represents the top reasons users reported for why their individual tasks were not completed on the promised dates. Resulting from a decade of capturing more than 22 terabytes of project data, Touchplan has the largest set of as-built construction data in the world.
Properly planning handoffs for Touchplan’s users has proven to reduce rework by 20% and planning-related project delays by 50%.
Tim Negris leads MSI’s marketing team to increase global visibility and demand for its award-winning services and software solutions. Negris began his career as the first product manager for what is now Microsoft SQL Server. Later, with Larry Ellison at Oracle, he conceived and led the introduction of “Thin Client” computing, a key precursor to the cloud. He also served as VP of Sales and Marketing for IBM software. Tim has a decades-long track record as a marketer and thought leader in introducing innovative solutions for real-time data management, advanced analytics, business process automation, and applied artificial intelligence to the world’s largest companies.
Jason Lyon serves the Customer Success team by enabling the group to deliver the immediate and lasting value of Touchplan to drive retention and expansion. He also works cross-functionally with the Sales, Product, and Marketing teams to advocate for customers. Jason joined Touchplan in 2018. He and the customer success team ensure construction teams have the support they need beginning with onboarding to make sure their user experience with Touchplan allows them to achieve all the construction goals.