The 2020 CURT Awards of Excellence
THE CONSTRUCTION INDUSTRY SAFETY EXCELLENCE (CISE) AWARDS
The Construction Industry Safety Excellence (CISE) Awards program was established to recognize commendable safety management and safety improvements of owners, constructors, and Local User Councils. Please join CURT in recognizing the recipients and honorable mentions from the 2020 Virtual Awards of Excellence Gala. Details on each project, photos, and quotes where available can be found below.
Congratulations to all! You truly exemplify the best of the best in terms of safety, project excellence, and workforce development, and CURT is proud to count you as part of the CURT community. For details on how to apply for the 2021 round of awards, please visit www.curt.org and click on the Awards tab to choose the category you are interested in.
2020 OWNER SAFETY AWARDS
Company-wide Project, Portfolio, or Program
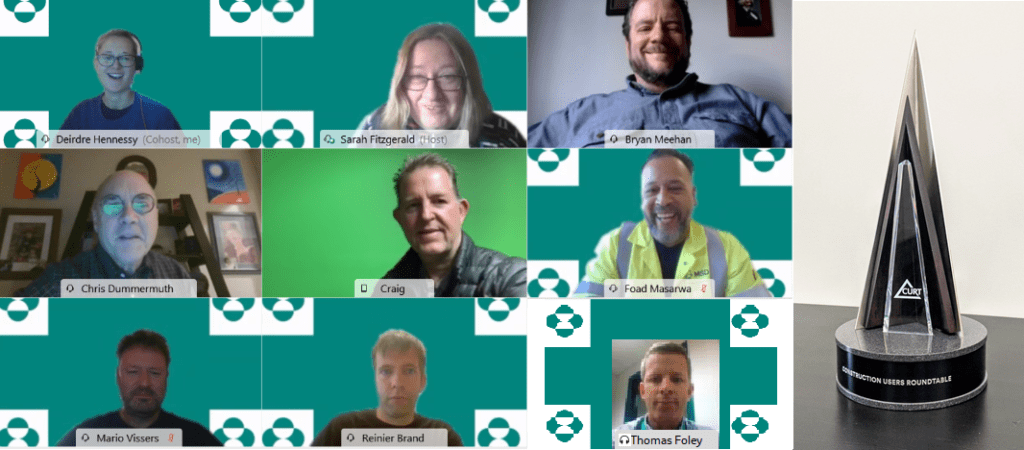
MSD-GES EMEA/AP
MSD has been in the business of saving and improving lives for more than 125 years by developing medicines and vaccines and conducting research to prevent and treat diseases.
From 2017-2019, MSD had several major projects in Ireland, Asia, and Continental Europe. These included MSD Dublin, Carlow 2, Brinny V116, Boxmeer SFFD, Krems Biotech, Igoville AH, Haarlem QC Lab, and Singapore Keytruda, Hangzhou Formulation. Throughout these projects, management demonstrated an unwavering commitment to the safety and well-being of its employees through weekly safety walks.
By targeting Zero Harm, Zero Defects to ensure the work was executed right the first time and implementing innovative solutions, such as Hypercare and Hearts and Minds, MSD completed these projects with an excellent safety record. Congratulations MSD.
“It is with great honor that the MSD EMEA/AP Project team receives this award,” says Chris Dummermuth, EMEA Director of Project Delivery. Over the past 10 years, we have had a steady improvement in enhancing the message of safety being a value in everything we do. Doing the work safely and right the first time is the most important part of doing the job well. Our CM and contractors working on our projects have adopted this approach, and it has led to a result of sending our workers home safe.”
Photo top row: Deirdre Hennessy; Sarah Fitzgerald; and Bryan Meehan. Photo middle row: Chris Dummermuth; Craig; and Foad Masarwa. Photo bottom row: Mario Vissers; Reinier Brand; and Thomas Foley.
Specific International More than 12 Months in Duration
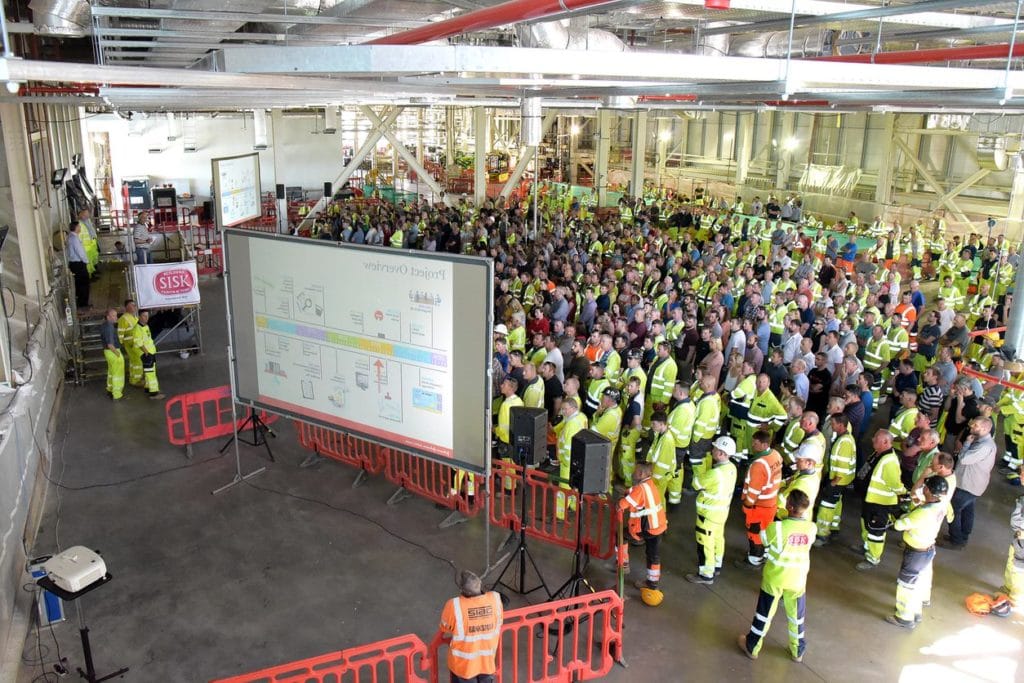
Janssen Sciences Ireland UC BioCork 2 Project
The Janssen Sciences Ireland UC construction work involved two distinct workstreams. The main expansion involved the construction of a new manufacturing building containing four large-scale production bioreactors. A second workstream included the expansion of an existing warehouse, a new high bay warehouse, a laboratory administration building extension, and a cafeteria extension, as well as support infrastructure and utilities.
The success of this project began with the appointment with a Safety Direct Responsible (DRI) to oversee all safety, health, and environmental conditions. A full-time safety advisor for every 20 workers and a robust safety management system ensured that subcontractors were fully aligned with the safety culture on the project. Innovative safety solutions, such as stand-alone portable acoustic cutting booths, reduced the risk of injury, which ultimately contributed to the excellent safety record for this project.
“One of the fundamental project goals was to guarantee that everyone – contractor, consultant, and employee – went home safe and well to their family each day,” says Jim Breen, Project Lead. “Everyone associated with the project was aligned on ensuring that this goal became reality. We are proud to have had a consistently strong safety record on a project that accounted for approximately 4.1 million people-hours and a peak site workforce of 1,300. The project involved more than 5,000 workers over the course of the project cycle with more than 80 subcontractors and equipment vendors from 40+ countries. This award truly belongs to everyone who worked on the project in Cork, Ireland.”
The photo shows Janssen Sciences’ Ireland UC BioCork 2 Project.
Specific US Project More than 12 Months in Duration

Exxon Mobil Global Projects Co. BLADE Project 2020
ExxonMobil Global Projects Company operates facilities all over the world, exploring for oil and natural gas on six continents. The Beaumont Light Atmospheric Distillation Expansion (BLADE) project employed over 1,800 personnel and recorded more than 2.2 million hours worked.
Five key BLADE behaviors included act, courage, care, respect, and recognize. These key behaviors were paramount to the safety of the project, along with innovative safety practices, such as the use of artificial intelligence (AI) for predictive data modeling and safety issue identification and virtual reality (VR) safety training. As a result, Exxon completed this project with zero recordable injuries! Congratulations, ExxonMobil Global Projects Company!
“We are honored to receive the CURT CISE Owner Safety Award,” says Terry Boles, BLADE project Executive, ExxonMobil. “This award is the result of hard work by dedicated project professionals committed to safety. The BLADE project team promoted an outstanding safety culture and created a safety vision that all of us can learn from and rally behind.”
The photo shows the BLADE project team.
2020 CONTRACTOR SAFETY AWARDS
NAICS 236 – General Building Contractors
Category 2 (Greater than 500,000 and Less than 3 Million Work Hours/Year)

Graycor Industrial Constructors, Inc.
Founded in 1921, Graycor Industrial Constructors is one of the nation’s largest planning, design/build, construction, and maintenance service groups. As an industry leader, Graycor adheres to its zero-incident program, which has become an industry-standard against which clients compare and judge their contractors. This systematic approach assures that safety goals are met through management commitment, endless training, proactive processes, and continuous improvement.
Graycor’s Safety and Health Management System is an integral part of how the company conducts business. The Graycor Safety & Health Manual, which is comprised of eight basic elements and 40 health and safety topical sections, aligns perfectly with the 16 Tactical Elements of the Construction Owners’ Safety Blueprint, with all elements and sections providing detailed guidance toward the goal of Zero Injuries. Strong programs and procedures, such as a mid-day Task Safety Analysis and the Serious Injury and Fatality Prevention (SIF) awareness and precursor identification, contribute to Graycor’s stellar safety performance.
“Graycor Industrial Constructors is very proud to be recognized for the third time as a CISE Award Winner (2016, 2018, and 2020),” says Sam Potter, GIC President. “While no company establishes safety programs and goals to win awards, to be recognized for the hard work and dedication to safety excellence we try and provide our teams is certainly gratifying. We are proud that the efforts of the entire company are being acknowledged from such a well-respected organization as CURT.”
The photo shows, from left to right: Pat Kouns, General Manager, Metals Divison; Shawn Anderton, Vice President and General Manager, Western Operations; and Kevin Grooms, Project Director, Gas Infrastructure & Power.
NAICS 237 – Heavy Construction Contractors
Category 1 (less than 500,000 Work Hours/Year)
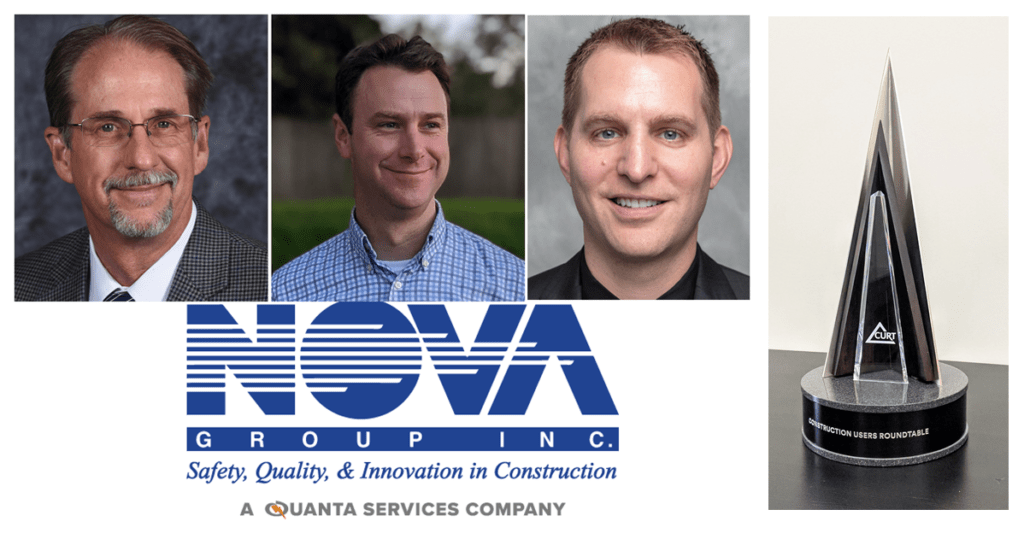
Nova Group, Inc.
Nova Group, Inc. (Nova) provides general engineering construction services to federal government agencies throughout the United States and internationally. Primary clients include the U.S. Navy (NAVFAC), the U.S. Air Force, the U.S. Army Corps of Engineers (USACE), the Department of Energy (DOE), and most recently, a private airport fueling project located at San Diego International Airport.
A VPP Star site at their steel fabrication facility in Napa, CA, and the recipient of the AGC of America Construction Safety of Excellence award, Nova’s safety program encompasses subcontractors, suppliers, and vendors, and is supported and enforced throughout Nova from the top down. Daily Stretch and Flex activities, daily huddles with an emphasis on RED (recognize, eliminate, and discuss), confidential safety flashes prepared for substantial incidents, and other practices weaved throughout Nova’s routine operations are key to their safety success.
“Nova Group is honored to receive this award,” says Cole Davis, Corporate Safety Director, Nova Group, Inc. “We appreciate the industry recognition for our continued safety commitment to our employees, who are our most valuable asset. Nova strives to pursue new and innovative practices and safety techniques, and sharing and collaborating to further both Nova and the construction industry as a whole.”
This photo shows, from left to right: Scott Victor, President and COO; Thiel Harryman, VP of Operations; and Cole Davis, Corporate Safety Director.
NAICS 237 – Heavy Construction Contractors
Category 2 (Greater than 500,000 and less than 3 Million Work Hours/Year)

W.T. Byler Co., Inc.
W.T. Byler Company has provided decades of service in heavy and civil engineering construction. They specialize in site-preparation, railroad construction, and railroad maintenance, dedicated to creating value for customers who depend on a turnkey solution with worry-free safety and reliability throughout the state of Texas and southwest Louisiana.
As the recipient of many safety awards, W.T. Byler has had zero lost-time incidents since August of 2015. W.T. Byler is committed to completing each project with an outstanding safety record, along with cost and schedule performance. Their Tracking Zero program embodies this commitment to every work-hour completed with zero accidents or incidents. They utilize safety slogans to keep safety in the mind of every employee, provide fleet training to their over-the-road truck drivers, and always use 100 percent PPE and JSAs.
As an Accredited Quality Contractor, W.T. Byler is committed to providing their clients with the highest quality construction services while caring deeply about their employees and the communities in which they build. W.T. Byler is committed to serving their communities and providing employees with the skills they need to work safely and productively.
“Winning this award means that our program is aligned with the clients,” says Wendell Rychlik, Executive Director. “It means that the ownership, management, and employees own the program and that safety has priority above production. We’re always ‘Tracking Zero.’”
This photo shows, from left to right: Geoff Pospisil, Director of Safety and Risk Manager; and Wendell Rychlik, Executive Director.
NAICS 237 – Heavy Construction Contractors
Category 2 (Greater than 500,000 and less than 3 Million Work Hours/Year)

Barriere Construction – Honorable Mention
Barriere Construction is a fourth-generation family-owned infrastructure construction services and materials-provider with a 71-year history of safely and reliably delivering quality industrial, private, and public works projects to loyal and new customers across the Gulf South. Barriere currently has 485 employees operating out of five groups strategically placed through the state to serve their customers. Approximately 60 percent of their work involves federal, state, parish, and municipal projects; and 40 percent involves private work in petrochemical facilities and commercial projects.
Barriere’s first and most important core value is the safety of their employees and the public entering their job sites. They are committed to an ongoing, comprehensive safety program, as well as a “zero-incidents” safety culture in which they believe that all incidents and accidents are preventable. This philosophy is clearly stated in Barriere’s Mission Statement and Core Values and is incorporated into their Health, Safety, and Environmental manual. Every Barriere employee is expected to take a “safety begins with me” attitude and be responsible for his/her own behavior.
Barriere has implemented “The 6” – a program that focuses on the core responsibilities of “The 6” indicators (new employees, safe zones, traffic control, utilities, heat stress, and lockout/tagout) to prevent serious injuries and fatalities. Each of “The 6” indicators is reviewed at the daily JSA meetings. Because of this, Barriere has achieved an excellent safety record.
Whether it is improving the parking lot at the Shell Norco Refinery, expanding the St. Charles Parish railyard at the Port of South Louisiana, or constructing secondary containment at Mosaic Fertilizer, Barriere has demonstrated an unrelenting commitment to the safety of its employees and clients.
“At Barriere, safety is a shared, uncompromised core value upheld through active executive and employee involvement,” says Les Mays, CSP, Safety Manager. “We prioritize empowering our workforce to drive a safety culture that we all own through a mutual journey to zero incidents. We know that zero-incidents is achievable, and earning a CURT CISE Award Honorable Mention is a sign that we are headed in the right direction. We appreciate the opportunity to evaluate our health and safety management systems through this award program, and we thank our customers and peers for recognizing our efforts.”
This photo shows, from left to right: Matthew Wilson, Director of Marketing, Communication, and Government Affairs; Peter Wilson, President/CEO; and Paul Albrecht, Sr. Director of Safety & Training.
NAICS 238 – Special Trade Contractors
Category 2 (Greater than 500,000 and Less than 3 Million Work Hours/Year)

United Group Services, Inc.
United Group Services, Inc. is an industrial construction firm headquartered in Cincinnati, OH that specializes in piping, rigging, insulation, fabrication, and managed maintenance. They market, sell, and operate their business based on their core values: safety, quality, and service.
United Group Services, Inc. maintains its safety culture in a variety of ways: three crew-centered safety meetings each day, safety task assessments, recognizing employees for simply making quick corrections, and providing reminders to their fellow employees (Brother’s Keeper), and the Extra Step program, which involves the identification and correction of hazardous conditions on any site, regardless if it is in their scope. United Group Services, Inc. held a Family Safety Day in July 2019 to show their families what they do and how they work safely, as well.
“Receiving the CURT CISE Award is a huge honor that was earned by every team member at United Group Services and represents true engagement of our craft professionals at each work face,” says Kevin Snell, CVO. “Unlike other awards received in a given year, the CURT CISE Award represents recognition from the user community, in other words, our customers, who support our efforts toward total employee health.”
This photo shows, top to bottom: Kevin Snell, CVO, and Dan Freese, CEO.
NAICS 238 – Special Trade Contractors
Category 2 (Greater than 500,000 and Less than 3 Million Work Hours/Year)

Starcon, a Cianbro Company – Honorable Mention
Founded in 1983, Starcon International, Inc. is a privately held full-service mechanical contractor offering comprehensive industrial and mechanical contracting services to a wide variety of process industry clients in the refining, chemical, food processing, metals, paper, and power industries. Starcon maintains a national footprint through its corporate headquarters in Texas and regional offices in Illinois, Kentucky, Louisiana, and Washington State.
Starcon’s safety management program is established in Starcon Standard Operating Procedures (SOPs) and Injury and Illness Prevention Program (IIPP). These include comprehensive requirements and guidance designed to assure compliance with regulations and company expectations to ensure the Starcon core value of maintaining a workplace where “No One Gets Hurt.”
Starcon’s world-class safety performance is the culmination of the company’s cultural commitment to safety, a forward-looking reliance on leading indicators, a variety of high-caliber HSSE initiatives, and most importantly, the daily commitment to safety by Starcon’s team members. Starcon’s emphasis on safety is nothing without team members who share its vision, take personal ownership of the process, and strive to go Beyond Zero. They are more than contributors to Starcon’s success – they are the cause.
“It’s a great honor to be recognized by CURT with this CISE Award,” says Peter Cinachette, President and COO. “This significant achievement could not have been realized without the hard work and dedication of our team members working together. Health and safety at Starcon has always been our highest value and this milestone is a testimony to the effectiveness of our safety program and culture. Congratulations to our team members across the company who earned this recognition and thank you for your commitment to safety excellence!”
This photo shows, from left to right: Peter Cianchette, President and COO; and David Folmar, Director of HSSE.
2020 ASSOCIATION SAFETY AWARDS

National Association of Women in Construction
The National Association of Women in Construction (NAWIC) provides education, support, and networking opportunities to help its members build their careers and technical skills in construction. Through its robust safety and health committee, and national alliance with OSHA, NAWIC spreads the message of safety and health through educational programs, conferences, social media, webinars, toolbox talks, and YouTube videos. NAWIC also recognizes excellence in safety through its awards programs for general contractors and subcontractors, and fully supports and promotes the tenets of CURT’s Owners’ Safety Blueprint through its safety and health committee and OSHA alliance.
“NAWIC has dedicated volunteers working in all facets of the construction industry whose core purpose is to strengthen and amplify the success of all women in our industry,” says Anne Pfleger, CIT, National President. “Receiving this prestigious award from CURT only further exemplifies NAWIC’s core purpose by recognizing women from the field to the board room who are not only dedicated to improving safety but have the continued energy to get involved in matters to make improvements that have an impact on all levels of our industry.”
From the left of the award, top to bottom: Anne Pfleger, CIT, NAWIC National President; Adair Stevenson, P.G., NAWIC Safety & Health Committee Chair; and Karen Brioso, past NAWIC OSHA Alliance Committee Chair. From the right of the award, top to bottom: Kathi Dobson, CSP, CHST, STS-C, LEED AP BD+C, Past NAWIC OSHA Alliance Committee Chair; Lauline Mitchell NAWIC National Vice President; and Crissy Ingram, NAWIC Executive Director.
2020 PROJECT EXCELLENCE AWARDS
Category 1 (Less than $50 Million)
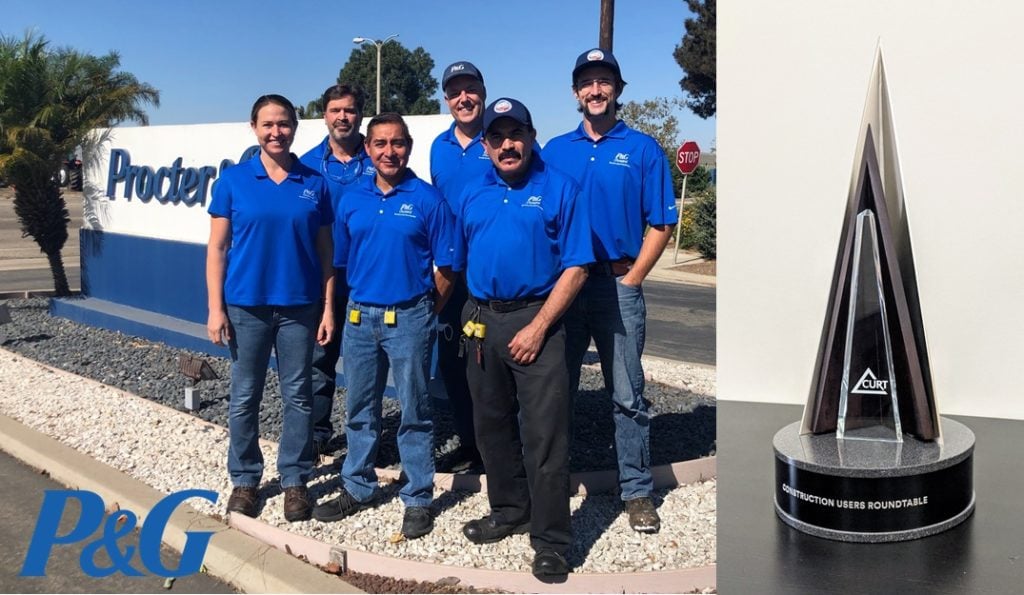
Procter and Gamble Oxnard Plant Optimus Project
Optimus, P&G Oxnard plan savings project scope was to close-couple palletization equipment to the production lines. Overall, the project is comparable to a “Game of Chess” – where pieces replace each other, and all moves coordinated while still operating the manufacturing business. All moves were completed with a minimum of operational downtime (12 days). This is the first major site project committed to a LEAN IPD execution method.
As part of the LEAN system, safety was the first Condition of Satisfaction from P&G and the first commitment from the contractors. Complete involvement throughout the project was critical and as a result of this focused effort, no injuries occurred across the project. The overall schedule hit all the milestones per the original project commitments. Four of the five major startups occurred within two weeks of the project funding plan adjusted by production planning and operations alignment.
Quality was actively managed; daily job walks with construction occurred. These checkpoints were utilized in the field to review the collaborative design and to verify that the installation would meet the overall intent and need. Follow-ups were recorded and posted in the BIG room for daily use and Q/A updates. A handful of RFIs were issued by construction for more detailed requests.
Both, P&G and their strategic partner, Spirit Construction, walked away very happy with the overall results. Feedback from Spirit, including their craft, was extremely positive. The plant operations and leadership team also were very impressed on the overall delivery and results to meet the project commitments. This clearly has become a model for how large expansive projects are planned.
No quote is available at this time.
This photo shows members of the Oxnard Plant Optimus Project team.
Category 1 (Less than $50 Million)

Flint Hills Resources/Turner Industries Group, LLC – Honorable Mention
Flint Hills Resources U21 Heater Replacement Project combined efforts of Fluor and Turner Industries Group, together with Insulations Inc. and Plaas Inc., who all worked together to deliver a project with a unique and impressive modular approach that allowed the team to overcome significant schedule challenges along with potentially crippling flooding threats to complete the project with essentially no quality defects. These challenges included working in narrow confined spaces on multiple levels at once, as well as amid rising water levels reducing the overall project timetable by six weeks. The project team was able to deliver maximum value to the project owner while maintaining a safe site that only had one weld that was required to be reworked, from over 300. Upon arrival at the destination, all modules fit perfectly together.
No quote is available at this time.
This photo shows members of the team.
Category 2 (Greater than $50 Million and Less than $1 Billion)
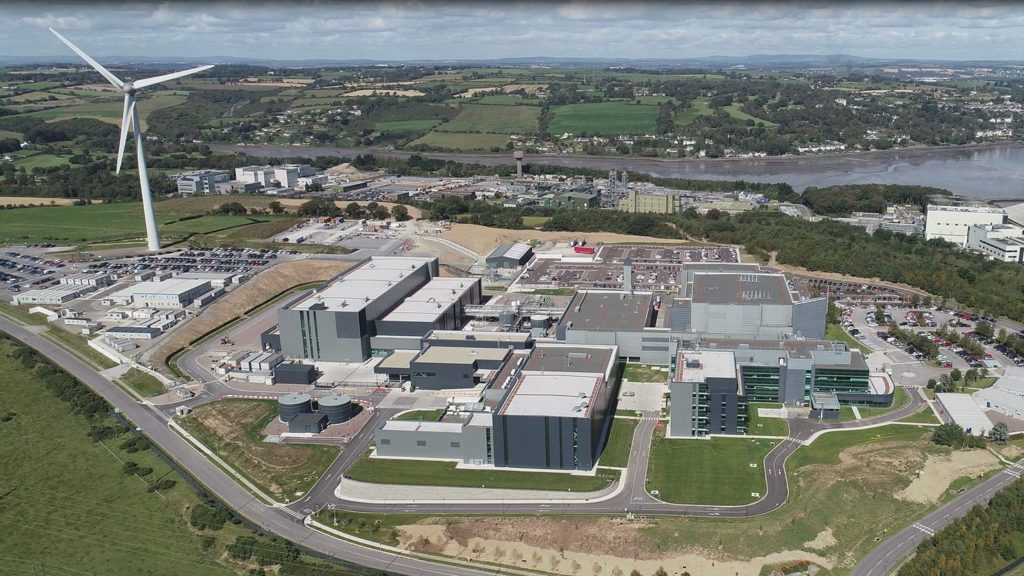
Janssens Sciences Ireland UC BioCork 2 Project
Janssen Sciences Ireland, part of the Johnson & Johnson Family of Companies, is at the forefront of treating, preventing, intercepting, and curing some of the world’s most devastating and complex diseases. The expansion of its existing manufacturing facility in Ringaskiddy, Co., Cork, Ireland incorporates large-scale fed-batch technology, which is the first of its kind in Ireland and for Johnson & Johnson. The project brought together Project Management Group (PM Group) and John Sisk and Sons for the completion of this effort. The project expanded the manufacturing space by 19,000 square meters, and further expanded the facility’s warehouse and administrative building and utility services.
With a commitment to safety second to none, the Janssen project team completed nearly four million hours with exceptional safety performance that incorporated best-in-class program elements. The project team was also able to deliver the project within the 22-month schedule by focusing on clear communication, not only within the project team but also with regular updates to external project stakeholders, with innovative communication methods. The project team was able to deliver the project below budget too, by strict adherence to change management and continuous administration of cost and value engineering opportunities.
The team’s commitment to quality was unparalleled, with the utilization of 3D and 4D technologies to conduct Process Hazard Analysis and virtual walkthroughs of both the process and construction plans. This allowed the team to efficiently preplan activities, which allowed for smooth execution.
The team embraced new technologies by integrating drone footage to improve visualization, 360-degree camera time-lapse footage for coordination, and Virtual Reality headsets for ergonomic studies and onboarding.
“At Janssen, we’re creating a future where disease is a thing of the past,” explains Jim Breed, Project Lead. “We’re the Pharmaceutical Companies of Johnson & Johnson, working tirelessly to make that future a reality for patients everywhere. We focus on areas of medicine where the need is high, the science is compelling, and the opportunity to make a difference is great. On behalf of our BioCork2 project team, we are delighted to accept a Construction Industry Project Excellence (CIPE) award. This award truly belongs to everyone who worked on the project in Cork, Ireland. Special recognition goes to PM Group, our engineering partner, and John Sisk and Sons, our construction partner. We would not have been in a position to receive this award without them, and sincerely thank them and their teams for helping us meet our objective to safely expand the Cork Biologics facility and ensure a sustainable supply of lifesaving medicines for our patients.”
This photo shows Janssen Sciences’ Ireland UC BioCork 2 Project.
Category 2 (Greater than $50 Million and Less Than $1 Billion)

TVA Construction/Barnard Construction Company, Inc.
After a 2014 Pickwick Landing Dam analysis revealed that the dam’s south embankment could face potential damage in a larger seismic event, TVA started making plans to stabilize the south embankment to meet dam safety criteria. Barnard Construction Company performed work on the dam’s upstream and downstream sides to provide stabilization, including constructing large buttresses, extended fills, and a new toe drain system while complying with the U.S. Army Corps of Engineers’ (USACE’s) requirements. This project required more than 1.9 million tons of import fill, sand, aggregate, and large rockfill materials, sourced from two river-based quarries and five land-based quarries. This required extensive coordination, scheduling, and communication.
Safety is a top priority in Barnard’s culture. All of Barnards’ supervisors complete an OSHA 30-hour training and TVA requires that all personnel working onsite complete an OSHA 10-hour training. Barnard conducted a monthly “Two Minute Rule Card” draw and required crew members to complete a Two Minute Rule Card when tasks changed; the purpose of these cards was to allow crew members to pause and survey their surroundings before beginning new tasks.
Adverse weather and flooding were major challenges that the project overcame. Barnard also experienced 72 additional weather days throughout the project. Despite these delays, Barnard completed the project five months ahead of schedule. They accomplished this by resequencing key activities, and efficiently collaborating (daily) with TVA and GEI Consultants, Inc. This allowed for a fluid and uninterrupted workflow; heavily focusing on grading fills to promote draining, and properly prepare work areas for rain events, and obtaining additional resources (field supervision and heavy equipment). The overall project savings were nearly $17 million, which was a result of successfully managing risk.
Barnard developed a grid layout at each fill source and tested materials from each grid months in advance to obtain approval. Barnard obtained samples in each grid and developed a detailed proctor selection process and followed the process in the field. GPS-equipped excavators tracked locations of dropped stone and where it was pushed to depth. The GPS also included a section view showing the bucket in relation to the estimated bottom of recent sediment. The team used control blocks and probing to confirm stone had reached the target depth. This construction technique is unique in that it can be used to stabilize an area or create a foundation in areas where dredging is restricted
“The success of the Pickwick Landing Dam South Embankment Seismic Upgrade Project was due to the collaboration and teamwork between TVA, Barnard, and all other parties involved,” says Quincy Anderson, P.E., Pickwick Project Team. “Winning the prestigious CURT CIPE Award was a well-earned affirmation of the success of this team. This project is an example of the success a project can achieve when all parties work together as a team. Winning this award provided confirmation to our team that we had completed a world-class project.”
This photo shows, from left to right: Alan Casaday, General Manager TVA; Kevin Holbrook, Senior Manager TVA; Jacob Horton, Construction Manager TVA; Justin Hays, Construction Manager TVA; Quincy Anderson, Project Manager Barnard; Brian Krohmer, Operations Manager Barnard; and Jerrod Deitchler, General Superintendent Barnard.
Category 3 (Greater than $1 Billion)

MSD
The MSD Biotech Dublin project involved the repurposing of MSD’s existing facility at Swords Co. Dublin for the manufacturing of biological drug substances. The project included repurposing the entire 33-acre site, including repurposing the existing 10,000 sqm warehouse into a production facility, repurposing the existing manufacturing space into a central utility building (CUB), and building a new QC laboratory.
The scale of this project required a joint venture to be established between two leading EPCM firms in Ireland, Jacobs Engineering and Project Management Group (PM Group). Additional challenges included an accelerated schedule (six months faster than similar projects in scale), a congested site and logistics, and limited craft and professional resources. Finally, the project was completed in the height of COVID-19 pandemic quarantines.
Safety is priority one for MSD. Four and a half million manhours were spent over the 2.5-year duration, without lost-time incident and impressive leading indicators. Additionally, the project team implemented the last planner system, along with several other initiatives, to drive the fast-track schedule without delay. The project team’s efforts allowed the project to complete within one month of the original aggressive schedule, even with significant COVID delays.
In order to stay on budget, the team adopted several target value delivery principles, including early onboarding of trade partners and budget transparency. The project was able to meet project cost targets.
To meet right-first-time quality objectives, the team implemented several programs, including digitized/paperless documentation records, digital three-stage safety inspections, and off-site fabrication with extensive digital pre-shipment checks.
The team’s efforts established new cultural norms that allowed for speedy issue resolution and collaboration as well as modular building principles that accelerated speed of delivery. The team established new benchmarks for future MSD project teams to strive towards.
“Our team is delighted and honored to receive the CURT Project Excellence Award,” says Mary Linehan, Director, Project Delivery, Global Engineering Services. “So many people have worked tirelessly to deliver this project while maintaining world-class safety, best in class quality, and a record-breaking schedule. It is fantastic that an organization like CURT has recognized everyone who worked on this project for their extraordinary efforts and dedication to deliver this project successfully with safety first and quality always as its core value.”
Photo top row: Tim Reilly; Chris Dummermuth; Brian Meehan; and James Croke. Photo bottom row: John Butler; John Tully; and Mary Linehan.
2020 WORKFORCE DEVELOPMENT AWARDS
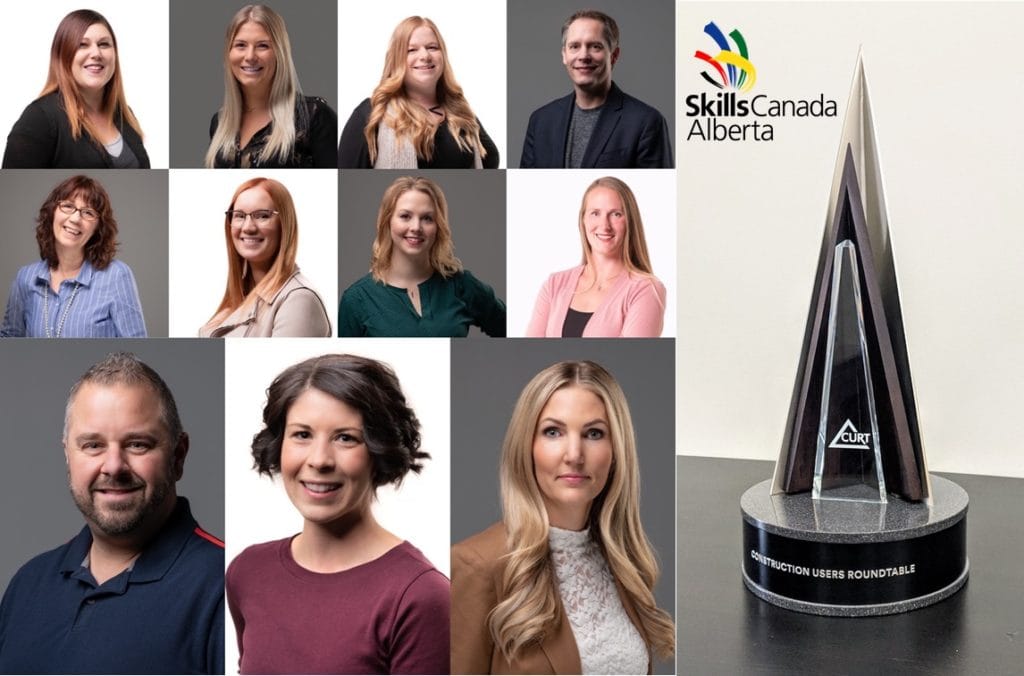
Skills Canada Alberta
Skills Canada Alberta established the Skills Exploration Days, which is a career awareness event that provides an opportunity for over 600 teachers and junior high students (Grades 7 to 9) to participate in an authentic and meaningful skilled trade and technology career exploration experience. Students across Alberta are introduced to the five stages of the design thinking process – empathize, define, ideate, prototype, and test. Prior to attending Skills Exploration Days, teachers are required to facilitate the empathy, define, and ideate phases of the students’ “pre-work” for the event during their regular class time.
During Skills Exploration Days, students tour a 38,000+ square foot facility and participate in skilled trade and technology career exploration experiences by visiting Learn-A-Skill stations. The Learn-A-Skill stations allow hundreds of students to explore their interests and passions as they rotate through hands-on stations that include the opportunity to work one-on-one with over 100 industry experts where they learn how to use tools, technology, and materials safely while also acquiring career-related skills and knowledge. The end goal is to encourage students to consider the many career opportunities provided through career and technology studies.
“On behalf of the Skills Canada Alberta team, I would like to thank the CURT panel for recognizing Skills Exploration Days,” says Becky Peterson, Education Coordinator for Skills Canada Alberta. “Winning the Workforce Development Award for this program has been a highlight of the year. The true winners of this award are all the volunteers and teachers whose hard work and dedication contribute to the success and growth of Skills Exploration Days. These industry experts help junior high school students learn about and appreciate careers in trades and technologies while getting tools into their hands and teaching them life-long skills.”
This photo shows, from left to right, top row: Ashley Carlyle, Office Coordinator; Amy Matthews, Partnership Coordinator; Whitney Koop, Provincial Competition Coordinator; and Chris Browton, Executive Director. Middle row: Karen Woitas, Partnership Lead; Victoria Anderson, Communications Coordinator; Katherine Kupchenko, Event & Registration Coordinator; and Randi Cox, Education Facilitator. Bottom row: Mike Sury, Manager of Programming & Resource Relations; Becky Peterson, Education Coordinator; and Alycia Pawluk, Manager of Programming & Education.
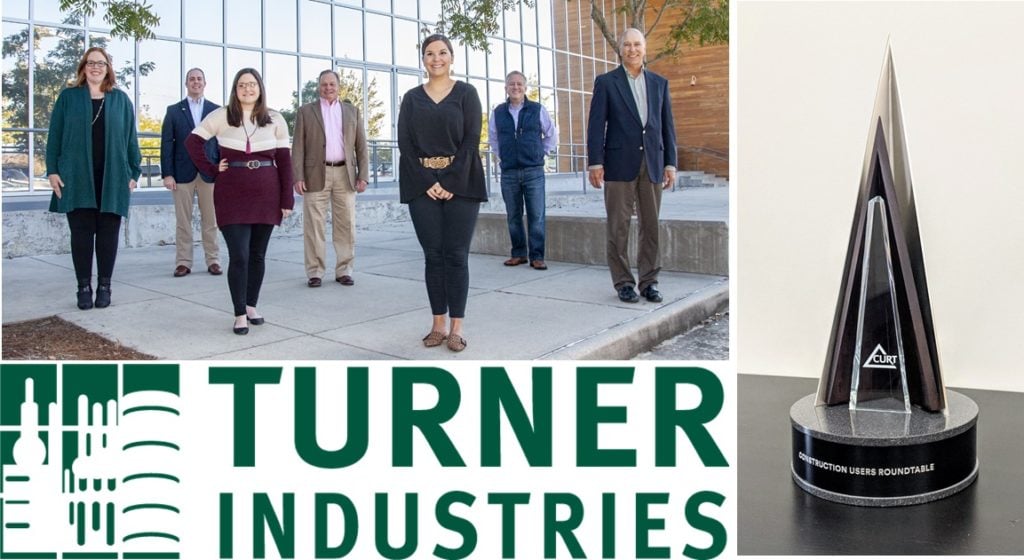
Turner Industries Group, LLC
Maximizing Louisiana’s Incumbent Worker Training Program to Expand Workforce Development Outreach at Turner Industries Group, is the tag line for this workforce development program. Louisiana’s Incumbent Worker Program (IWTP) has offered employers the opportunity to reclaim unemployment insurance contributions in the form of training for their incumbent employees.
Turner Industries partners with Louisiana State University (LSU) Online and Continuing Education and several industry-specific vendors to deliver continued learning in the forms of leadership training, skills upgrade, Certified Occupational Safety Specialist (COSS), and Certified Occupational Safety Manager (COSM) classes for safety professionals among other types of training. The recent grant cycle provided $749,303.50 in state funds for training.
In addition, Turner Industries provided $111,998.00 to co-fund classes that are not fully eligible for grant funding. With this program, their goals were to create 79 additional jobs, retain 774 employees, and experience an average wage increase of 6% for program participants. The program created 81 jobs, 746 program participants (96.38%) were retained, and average wages increased by 8.24%. Due to the integration of the IWTP into their workforce development program, Turner Industries improved the knowledge and skills of their workforce, creating opportunities for advancement, and achieved a 300% return on investment in 2019.
“Turner’s goal is to maintain a world-class workforce development organization for the industrial maintenance and construction market,” says Ray Neck, Director of Workforce Development, Turner Industries Group, LLC. “Winning this award for the fourth time validates our belief that we have achieved that goal. We are proud to be a part of a company that places such a high priority on Workforce Development and are thankful to CURT for recognizing our hard work.”
This photo shows, from left to right: Elizabeth Beckham; Bryan Gerace; Catherine Glueck; Wayne Tyson; Brooke Roussel; Stephen Toups; and Ray Neck.

The District of Columbia Water & Sewer Authority – Honorable Mention
DC Water Works has multiple large-scale infrastructure projects to upgrade its facilities and distribution system over the next 10 years, totaling billions of dollars. Recognizing that these projects are taxpayer-funded, the Water Works Initiative was launched to ensure local residents would be hired by the contractors working on these projects. This initiative established a goal that 60 percent of contractor new hires would be local.
To achieve this, DC Water partnered with multiple local agencies and organizations to forecast contractor hiring needs, identify potentially qualified candidates, establish a new registered apprenticeship program, and they had their contractors create mentoring and internship programs. So far, over 307 contractor positions have been filled with local residents. Because of the success of the program, the local hiring goal has been raised from 60 to 75 percent.
“On behalf of David L. Gadis, CEO and General Manager, DC Water would like to thank the Construction Users Roundtable (CURT) for this prestigious honor,” says Sharon Talley, DC Water. “This recognition affirms DC Water’s efforts to provide job training and employment to residents who live within the District of Columbia and the Authority’s surrounding User Jurisdiction. The Water Works Team firmly believes that this achievement would not be possible without the residents’ participation in our training and job placement programs. They are the real winners and we accept this award on their behalf.”
In this photo, from left to right: Jerrod Talley, Quality Assurance Apprentice; Jamal Jones, Compliance Officer; Andre Wonson, Water Utility Services Apprentice; Breona Carpenter, Quality Assurance Apprentices; Sharon Talley, Compliance Officer; and Richard Salmon, Water Utility Services Apprentice. (Not shown: Korey Gray, Director, Compliance and Business Development; Linda Fennell, Compliance Officer; and Albert Slack, Compliance Officer).

Worley – Honorable Mention
Research, Recruit, Develop, and Retain are the Four Pillars of Worley’s Workforce Development Program. The Pillars provide a framework around which they have designed a comprehensive workforce strategy that encompasses the development, implementation, on-going analysis, and continuous improvement of a multitude of workforce development initiatives, intended to work collaboratively to provide opportunities to find, hire, up-skill, and retain the best construction workforce in the industry.
Worley’s Workforce Development Team works closely with their Human Resources (HR) and Operations groups as employees move through their career life cycle. They work with the Operations teams to provide forecasts on upcoming project labor needs and employment opportunities. Their strategic outreach program identifies local talent pools and collaborates with HR to recruit and hire qualified applicants. Once onboard, they team up with on-site personnel to engage their employees through Progression Programs and Achievement Recognition Initiatives in order to celebrate their accomplishments internally and externally.
Worley believes that implementing a robust well-designed workforce development initiative produces a good return on investment. This belief was validated on a large capital project in an area that had an extremely tight labor market, high turnover rates, unacceptable historical safety performance, schedule slippage, and cost increases. Implementing their workforce development program reduced turnover rates, absenteeism, and TRIR, and increased performance/productivity on a $500 mm project. These improvements were calculated to reduce installed labor cost by 10 percent with the savings passed on to the client.
No quote is available at this time.
This photo shows members of the team.
THANK YOU TO EVERYONE WHO SUBMITTED APPLICATIONS FOR THE 2020 CURT AWARDS. PLEASE CONSIDER APPLYING FOR THE 2021 ROUND! DETAILS AND DEADLINES WILL BE ANNOUNCED SOON!
Connect with CURT to stay up to date on everything construction related. Link up with us on Facebook and LinkedIn for more great content that will help you lead your team and succeed in your position.
CURT’S MISSION IS TO CREATE A COMPETITIVE ADVANTAGE FOR CONSTRUCTION USERS. CURT ACCOMPLISHES THIS MULTIFACETED OBJECTIVE BY PROVIDING AGGRESSIVE LEADERSHIP ON THOSE BUSINESS ISSUES THAT PROMOTE EXCELLENCE IN THE CREATION OF CAPITAL ASSETS.